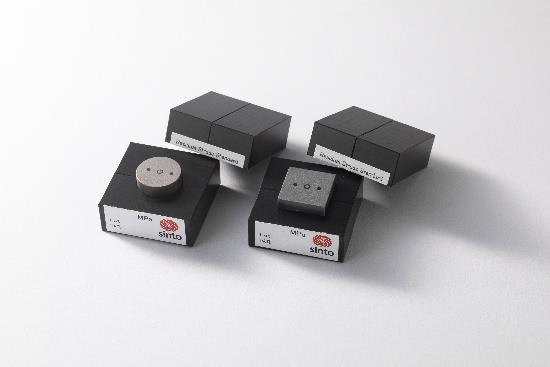
Calibration standards are critical for ensuring accurate measurements of residual stress. They are physical specimens or materials that serve as benchmarks, allowing for the validation and adjustment of measurement equipment to produce reliable data when testing. Accurate calibration is essential, as it directly impacts the assessment of material properties, which is crucial in applications where a precise understanding of material behavior is necessary for safety and performance.
Table of Contents
Calibration Standards for Residual Stress Testing
Calibration Standard Requirements
- The standard must have fine and uniform grains.
- The standard must be carefully stored and shipped. Fine particle powders are hazardous materials and can cause dust explosions.
- The standard must be kept in stable condition to prevent rust or contamination.
Preparing & Testing a Calibration Standard
The process for making a calibration standard is highlighted in ASTM E915. While this process was originally designed for sin2𝜓 equipment, it also applies to cosα machines. The process is defined below:
- Select a suitable method that does not induce residual stress in the binder. Methods could include:
- Creating a diluted formula of nitrocellulose cement (10%) and acetone, placing several drops on a sample tray or microscope slide, and sprinkling iron powder (greater than 1 µm) on top of it. Once the powder spreads and the powder and binder are uniform, the specimen must dry for several hours. The surface of the specimen must be flat, uniform, and clearly defined.
- Placing a small amount of petroleum jelly on a slide, flattening it with a second slide to create a uniform surface, then sprinkling the iron powder onto the petroleum jelly. When adding the powder to the slide, hold the slide vertically and sprinkle the powder from above the slide to prevent the powder from packing and building up.
- Ensure the surface area of the calibration standard is large enough to intersect the entire incident beam.
- Once the standard is dry, position it on the machine’s apparatus.
- Align the X-ray diffraction instrumentation per manufacturer guidelines to ensure the coincidence of specific axes and proper positioning of the X-ray beam and calibration standard.
- Perform five consecutive stress measurements (use manufacturer’s instructions).
- Analyze the data from these measurements and calculate the mean and standard deviation for all five measurements. Calibration is successful if the mean value is within 14 MPa (2 ksi) of zero. If the mean value is more than 14 MPa (2 ksi) of zero, check the machine’s alignment or you must create a new calibration standard and start the outlined process again.
Important Note: In addition to preparing and using calibration standards, it’s critical to inspect the condition of your machine daily. Routine inspections guarantee the precision and reliability of stress measurements. The inspections should ideally be performed at the start and end of each day.
Pulstec’s Calibration Standard
When you purchase Pulstec’s XRD Analyzer, you will not need to create a calibration standard. You will receive a stable calibration standard made from consolidated materials. The standard is not required to be enclosed in special packaging when shipped.
Reference Specimens
Generally, calibration standards and reference specimens do not need to be made from the same material. However, when measuring residual stress, using a calibration standard with a crystal structure and composition similar to the reference specimen can be important to ensure factors like diffraction angles and intensities are comparable.
Specimen Requirements for Residual Stress
Residual stress reference specimens must:
- Have a uniform surface level of residual stress.
- Have stable residual stress levels over time.
- Remain in stable conditions, with no rust or contamination.
Reference specimen requirements also depend on the targeted residual stress level. Select one that is close to the target residual stress level. Reference specimens can be as-built or created with heat treatments or cold working processes like shotpeening.
The reference specimens also comes with reference residual stress numbers, which you will use as target values for confirmation.
For Retained Austenite
There are two primary types of reference specimens for retained austenite measurements: consolidated powder and heat-treated. Consolidated specimens are more commonly used in materials analysis because, over time, heat-treated specimens may have varying retained austenite percentages.
Consolidated
Consolidated powder specimens are made from a mix of ferrite powder and a specific percentage of austenite powder, which is then consolidated by pressure to ensure a consistent and homogenous material structure. This uniformity is crucial for accurate X-ray diffraction measurements of retained austenite. The consolidation process ensures the reference specimen accurately represents the material’s properties without introducing additional variables that could affect the measurement, such as variations in grain size or composition that might occur in bulk specimens.
General requirements for consolidated powder specimens include:
- The grains must be fine and uniform.
- The surface must remain stable over time with no rust or contamination.
- It must be kept safe in storage and shipping to prevent dust explosions.
Heat-Treated
If you need to use bulk specimens for retained austenite measurements, use heat-treated specimens instead of consolidated powder specimens because they closely replicate the microstructural characteristics of real-world materials. These specimens are subjected to specific heat treatment processes to alter their microstructure, including the amount of retained austenite.
The most widely used material in bulk heat-treated specimens is SKD11, which is tempered at a lower temperature and provides more stable retained austenite percentages over time.
General requirements for heat-treated bulk specimens include:
- They must have low texture/uniform grains.
- Retained austenite percentages must be uniform at the surface of each specimen.
- Retained austenite percentages must remain stable over time.
- They must be stored in a controlled environment to remain stable.
- They must never develop rust or be introduced to contaminants.
Learn More From Pulstec
Founded in 1969, Pulstec manufactures X-ray measurement equipment, including the μ-X360J, a non-destructive, portable machine that can measure residual stress in 40 seconds and retained austenite in 90 seconds. You can use the μ-X360J for on-site measurements or integrate it into automated measurement systems.
Please contact us today to learn more about the μ-X360J or visit our resource library for more information about measuring retained austenite and residual stress.