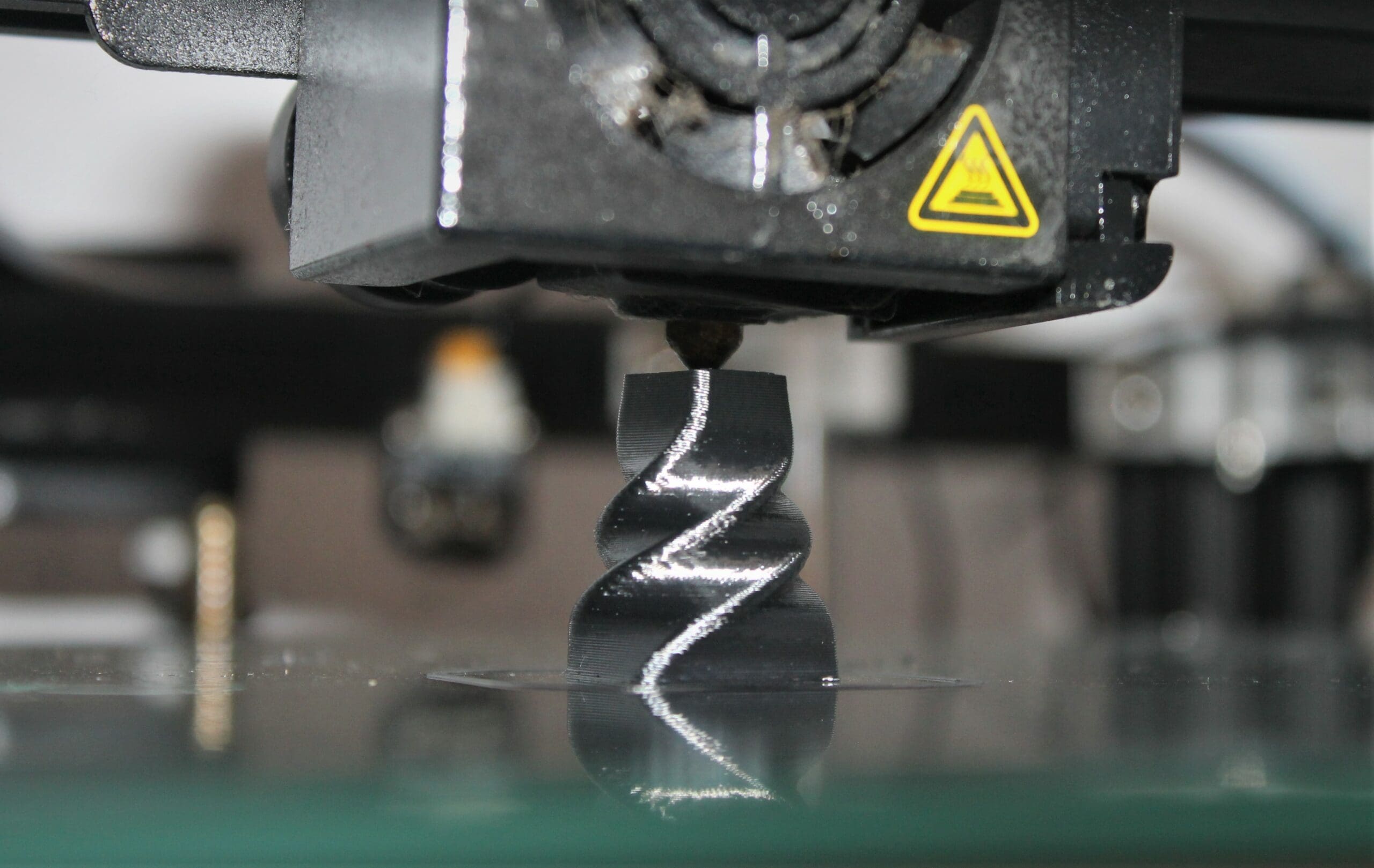
Table of Contents
Although additive manufacturing (AM) isn’t a new process, it’s a constantly evolving one. Since its inception, additive manufacturing has helped manufacturers achieve better process flexibility and efficiency, as well as create cost-effective prototypes. Despite the many benefits of additive manufacturing, there are still some critical challenges that need to be overcome, including controlling and reducing residual stress in AM components.
What Causes Residual Stress in Additive Manufacturing?
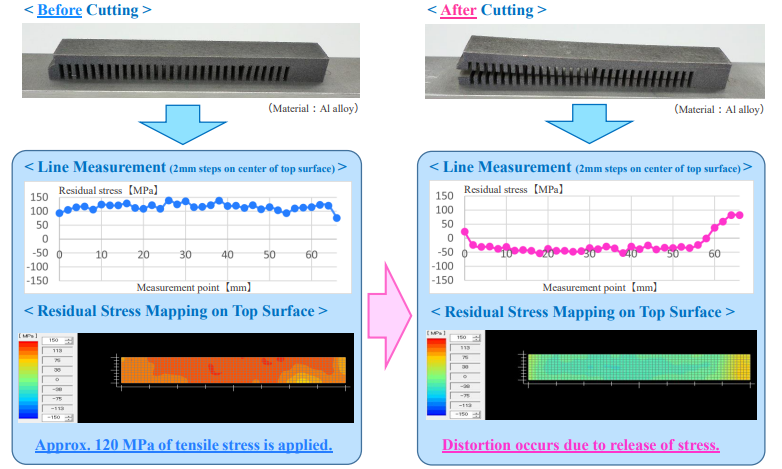
Residual stress in 3D-printed steel and other AM-produced parts is primarily caused by their thermal cycle during the rapid heating and solidification process.
According to the Journal of Manufacturing and Materials Processing, the primary factors contributing to residual stress include the maximum temperature difference, deposit height, substrate stiffness, energy density, and part geometry.
The maximum temperature difference refers to the temperature of the AM bar and the base bar during thermal cycling and, depending on this delta, affects the residual stress within the AM part. If the entire substance is preheated before AM, the maximum temperature gradient (MTG) may be reduced, impacting the stresses within the object. If temperatures are too high, microstructural coarsening can lead to poor mechanical properties.
Scan patterns can also affect residual stress within additive manufacturing produced parts, with Island scan patterns resulting in lower stress levels than alternative scan patterns. Additionally, a Residual Stress Development, Prevention, and Compensation Study published in 2020 found that energy input affects residual stress formations, with slower scanning speeds resulting in more residual stress.
The Effects of Residual Stress in 3D-Printed Components
Additive manufacturing allows the production of complex, varying geometries much quicker than traditional methods, but what effects do residual stresses have on these components?
Researchers who conducted a study on Residual Stress Development in Metal Additive Manufacturing found that the types of stresses found at the very center of AM-produced parts are typically compressive stresses, while the top layers of AM parts typically feature tensile stresses.
Compressive stresses, due to forces pushing in on an object, are beneficial for AM parts and make them stronger and more durable over time. Tensile stresses, on the other hand, can affect a part’s fatigue life and properties, increasing its chances of cracking, deformation, and total failure.
Identifying & Measuring Residual Stress
Even though there are a variety of ways to identify and measure residual stress in 3D-printed steel and within AM parts and components, some methods are more ideal than others depending on the use case and type of part being examined. If you’d like to learn more about some of the destructive and non-destructive methods used to measure residual stress, read our Residual Stress Measurement Guide.
Out of all the various measurement methods available, X-ray diffraction (XRD) is one of the best ways to identify and measure these stresses safely and consistently. X-ray diffraction is a fast, safe, and non-destructive method, so you won’t have to worry about damaging your component during the measurement process.
XRD analyzers work by using a zero-, one-, or two-dimensional sensor to measure either part or all of the Debye-Scherrer ring, allowing the observation of peak profiles within certain sections of the ring. Using Bragg’s Law, strain can be calculated from the ring’s positions.
Can Residual Stress Be Prevented in AM Parts?
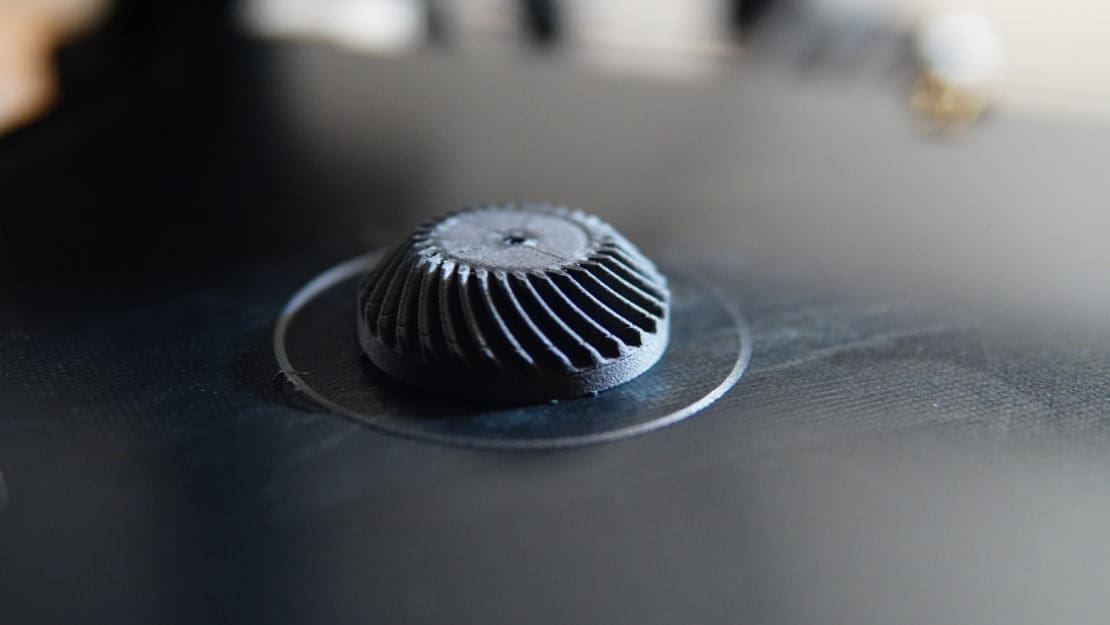
While it is difficult to prevent residual stresses in AM parts completely, there are several methods that could be used to reduce the amount of stress present within the solidified and cooled object.
In the Journal of Manufacturing and Materials Processing, a study was published in 2021 by Xufei Lu, Miguel Cervera, Michele Chiumenti, and Xin Lin. This study mentions that some of the best stress control methods include:
- Preheating the substrate or material before the AM process
- Laser or shot peening
- Reducing the maximum temperature gradient
- Heat treatments
Researchers Kevin Carpenter and Ali Tabei also suggested in their 2020 study that AM stresses could be prevented by:
- Lowering heat inputs
- Decreasing laser height and laser power
- Modifying and adjusting scanning speeds and laser power, optimizing for higher scan speeds, and lowering laser power values to reduce residual stresses
Due to the large variety of additive manufacturing techniques available, techniques and strategies to lower residual stresses will vary. This continues to be a widely researched topic, and more studies will need to be completed on residual stress prevention to find the optimum methods for each particular AM use case.
Learn More About Measuring Residual Stress in 3D-Printed Steel & AM Components
Pulstec is an electronic equipment manufacturer that has developed a wide range of innovative products, including the XRD analyzer which can measure both residual stress and retained austenite amounts in polycrystalline material. Our non-destructive XRD analyzer is incredibly fast (results within 40 seconds), lightweight, and uses a two-dimensional sensor to display the full Debye-Scherrer ring. You can learn more about how our analyzer works here.
If you have questions about measuring residual stress in 3D-printed steel and AM components, or you would like to request a free demo of our analyzer, please contact us today.